目前國家的技術(shù)政策中推薦采用厭氧消化工藝對污水處理廠污泥進行減量化和穩(wěn)定化處理,但在厭氧消化過程中除產(chǎn)生甲烷外,還會釋放高濃度的氮,這部分高氨氮隨脫水濾液回流到污水處理系統(tǒng),增加污水處理的投資和運行費用。北京某污水處理廠采用厭氧氨氧化工藝對高氨氮污泥脫水濾液單獨集中處理,可解決上述問題。
北京市某污水處理廠泥區(qū)在優(yōu)化改造中面臨諸多問題,其中沼液處理問題直接影響了該廠污水處理的效果和成本。熱水解和厭氧消化后的污泥經(jīng)脫水后產(chǎn)生脫水濾液(沼液),該濾液中氨氮濃度較高,如果不進行處理直接排至廠區(qū)生物處理系統(tǒng),將對再生水處理工藝中總氮的出水指標造成一定的影響,使污水中碳氮比不足的問題更加突出,增加大量的碳源投加量,增加污水處理的難度和處理成本。因此有必要將這部分污水單獨收集處理,以減少這部分污染物對污水處理設施的沖擊以及系統(tǒng)的氮負荷。
脫氮技術(shù)中,厭氧氨氧化技術(shù)作為新興工藝,克服了諸多傳統(tǒng)脫氮工藝的缺點,受到了普遍關(guān)注。因此,在本設計中,如何選擇最優(yōu)技術(shù)路線以及在原有研究基礎上進行設計優(yōu)化是設計人員需要解決的主要問題。
1厭氧氨氧化工藝的優(yōu)點
厭氧氨氧化工藝相比于傳統(tǒng)的硝化反硝化工藝具有如下優(yōu)點:
(1)節(jié)省能源和碳源:厭氧氨氧化在缺氧條件下進行,無需氧氣的供應,可節(jié)省62.5%的能源消耗;并且厭氧氨氧化過程徹底改變了過去需要通過投加電子供體(碳源)才能脫氮的傳統(tǒng)途徑(反硝化),大大節(jié)省碳源;此外能量減少也意味著CO2排放的降低。
(2)不會產(chǎn)生pH下降因而無需補堿,不存在亞硝酸鹽的累積可能產(chǎn)生的毒性,因而容易經(jīng)濟地實現(xiàn)工藝控制。
(3)減少污泥產(chǎn)量:厭氧氨氧化菌生長慢、產(chǎn)率低,工藝剩余污泥量少,因此污泥處置費用低。
(4)高負荷,減少占地面積:厭氧氨氧化氮去除效率高,因此該工藝總體負荷高,可以減少工藝占地,降低工藝基建費用。
2工程設計
2.1
工程概況
北京市某污水處理廠處理規(guī)模為60萬噸,污泥產(chǎn)量約為878噸/日,同時接收其他廠外運污泥342噸/日,總處理規(guī)模1220噸/日(以含水率80%計,不含廠內(nèi)污泥系統(tǒng)回流量),污泥處理工藝采用濃縮+預脫水+熱水解+厭氧消化+板框脫水(見圖1)。剩余污泥進入污泥濃縮、預脫水系統(tǒng),經(jīng)過濃縮機濃縮后,與經(jīng)過除砂的初沉污泥混合,利用預脫水機脫水與外廠輸送的脫水污泥混合后進入熱水解系統(tǒng)。熱水解處理后的污泥經(jīng)過
稀釋及冷卻后,進入新建的污泥消化池進行厭氧消化。消化后的污泥經(jīng)板框壓濾脫水系統(tǒng)進行脫水至含水率60%以下。脫水后泥餅外運處置。
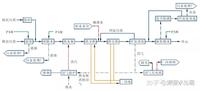
圖1 污泥處理流程圖
污泥處理過程中產(chǎn)生的污水包括污泥濃縮上清液、熱水解消化污泥脫水的濾液。污泥濃縮的上清液中主要含有部分SS; 污泥在經(jīng)過20多天厭氧消化后,大概24%的微生物被降解,每降解1kg微生物產(chǎn)生0.124kg氮,因此部分氮磷又被釋放到污泥脫水的壓濾液中,有關(guān)數(shù)據(jù)顯示,經(jīng)過厭氧消化后污泥水中氮的含量約占進水污水氮含量的10%左右,常規(guī)設計中回到污水處理系統(tǒng)會加重污水廠的負擔,因此需要對污泥脫水的壓濾液進行單獨處理。
本工程厭氧氨氧化系統(tǒng)設計規(guī)模(平均流量)為3500m3/d,根據(jù)中試和國內(nèi)外相近工程水質(zhì)數(shù)據(jù),確定了厭氧氨氧化系統(tǒng)進出水水質(zhì)(見表1)。
表1 厭氧氨氧化系統(tǒng)設計進出水水質(zhì)
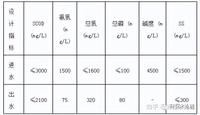
2.2技術(shù)路線
根據(jù)經(jīng)驗水質(zhì)數(shù)據(jù),最初選定技術(shù)路線為進水—調(diào)節(jié)池—斜板沉淀池— 一段生物池— 一段沉淀池—二段生物池—二段沉淀池—出水。脫水后的污泥消化液中除氨氮濃度比較高外,還有較高TP、SS、COD,為了保證反應器的脫氮效果,在前端增加混凝沉淀處理單元,去除TP、SS。然后進入一段生物池和一段沉淀池,去除COD。將TP、SS、COD去除后進入二段生物池和二段沉淀池進行脫氮。通過中試運行結(jié)果發(fā)現(xiàn),對于C/N比不高的污水,一段反應池的COD去除率在20-30%之間,此工藝流程僅適用于C/N比高的污水。
因此,針對某污水處理廠熱水解消化污泥脫水濾液的水質(zhì),將工藝流程優(yōu)化為進水—調(diào)節(jié)池—斜板沉淀池—生物池—沉淀池—出水(見圖2)。脫水濾液通過重力流方式進入調(diào)節(jié)池,完成水量與水質(zhì)的均化后,通過進水泵輸送至斜板沉淀池,在斜板沉淀池中去除TP、SS和部分COD,上清液通過重力流入生物池,在生物池中完成氨氮與總氮的自養(yǎng)去除。生物池內(nèi)的泥水混合物自流進入沉淀池,通過重力沉降作用泥水分離,上清液作為本系統(tǒng)出水排放至廠內(nèi)退水管線。
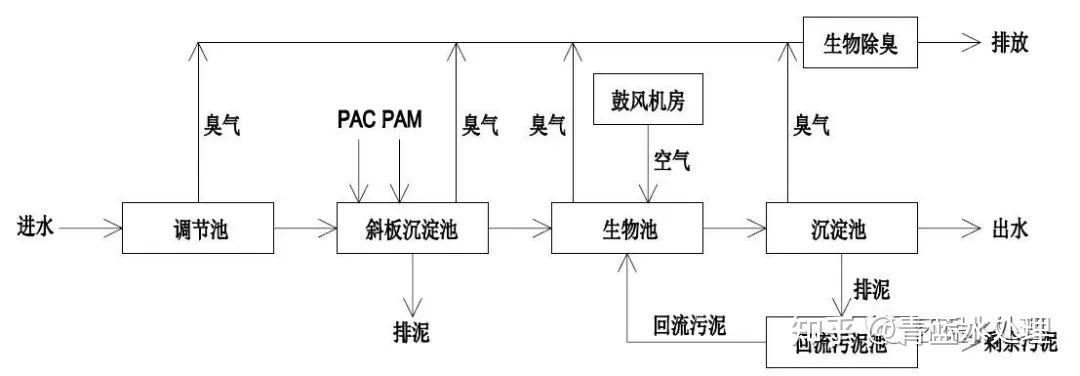
圖2 厭氧氨氧化系統(tǒng)工藝流程
2.3
厭氧氨氧化系統(tǒng)設計
厭氧氨氧化系統(tǒng)包含調(diào)節(jié)池、斜板沉淀池、生物池、沉淀池、鼓風機房。系統(tǒng)主要設計參數(shù)見表2。
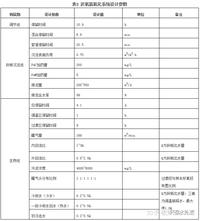
3
預期效果
厭氧氨氧化工藝處理脫水濾液在國內(nèi)外已有較多成功的實例,荷蘭鹿特丹污水廠已建厭氧氨氧化系統(tǒng)設施,設計處理規(guī)模為500 m3/d,進水氨氮濃度為800~1000mg/L,經(jīng)處理后出水氨氮20mg/L、硝酸鹽100mg/L,氨氮去除率90%,總氮去除率75%。本工程目前尚處于調(diào)試運行階段,大概需要6個月運行周期。但該廠的核心工藝“紅菌”已在高碑店廠啟動示范工程,用于處理水廠高濃度氨氮的消化污泥脫水濾液,處理規(guī)模500m3/d,經(jīng)處理后總氮去除率達到80%以上。且厭氧氨氧化工藝的核心工藝“紅菌”同樣應用于湖北省十堰市西部垃圾填埋場垃圾滲濾液處理,處理規(guī)模150m3/d,進水氨氮1000~1200mg/L,經(jīng)處理后出水氨氮小于10mg/L、總氮低于40mg/L
4
問題及優(yōu)化措施
4.1
問題
(1)厭氧氨氧化工藝啟動緩慢,世界上第一座生產(chǎn)性裝置啟動時間長達3.5年,過長的啟動時間是其工程應用的重大障礙。
(2)厭氧氨氧化菌(紅菌)生長緩慢,細胞產(chǎn)率低,且沉降性能不佳,易流失,反應器內(nèi)的生物活性不易維持。如圖3所示,為反應器運行不善,漂浮在水面上的紅菌。
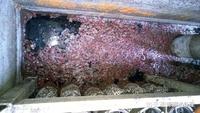
圖3 生物池內(nèi)紅菌
(3)厭氧氨氧化菌(紅菌)對環(huán)境溫度要求苛刻,這也是國內(nèi)厭氧氨氧化工藝大多停留在小試階段的原因之一。因此在工程化應用中,如何控制反應器溫度,保證系統(tǒng)穩(wěn)定運行,是設計者亟需解決的問題。
(4)厭氧氨氧化系統(tǒng)進水來自板框壓濾水,板框系統(tǒng)在長期運行之后,濾布很容易出現(xiàn)問題。一旦濾布泄漏,會導致整個厭氧氨氧化系統(tǒng)的進水SS升高,長期運行會使調(diào)節(jié)池底部沉泥增加,常規(guī)設計中檢修調(diào)節(jié)池需要整個厭氧氨氧化系統(tǒng)停產(chǎn),板框壓濾水再次回到進水泵房,從而影響后續(xù)的污水處理。
4.2
優(yōu)化措施
(1)系統(tǒng)在運行過程中,為保證系統(tǒng)內(nèi)部的生物量,沉淀池進水分布管處采取截面1/4開孔措施,使水流均布進入沉淀池,防止因集流進入導致沉淀池底部沉泥被攪起,從而影響回流污泥量;沉淀池出水槽兩邊加擋板,由于紅菌菌種顆粒小,沉降性能弱,易流失,擋板可以有效地在出水端截留污泥量,保證出水水質(zhì);沉淀池的剩余污泥在一般設計中會排入廠區(qū),本設計中,采取延長排泥時間措施,剩余污泥進入生物池,以回收菌種。
(2)為控制菌種溫度環(huán)境,設計中在生物池前端設置調(diào)溫池,經(jīng)熱量平衡計算發(fā)現(xiàn),冬季該廠生物池進水平均溫度為33℃,夏季進水平均溫度為37℃。紅菌最適宜生存溫度為35℃。所以將斜板沉淀池出水、初沉池水、冷卻水(冷水)及一級冷卻水回水(熱水)分別匯入調(diào)溫池,其中初沉水作為營養(yǎng)水。冷熱水通過潛水攪拌器攪拌混合,該混合水即為調(diào)溫水又為稀釋水,通過自動溫控系統(tǒng)調(diào)節(jié)流量,使水溫穩(wěn)定。該優(yōu)化措施同時利用了熱水解系統(tǒng)的低溫熱交換水(一級冷卻水回水),避免了能源浪費。