耐火澆注料應(yīng)用范圍比較廣,目前主要使用在煉鐵高爐等熱工設(shè)備內(nèi)襯及化工行業(yè)各種窯爐,及其他一些形狀復(fù)雜難以砌磚的部位。澆注料具有較高的耐火性能、良好的熱震穩(wěn)定性,并具有一定的抗硫酸鹽侵蝕性能。其使用溫度一般在 1350℃-1400℃,正常使用壽命一般在一年以上下面分析了煉鐵高爐用耐火澆注料損壞的常見原因。
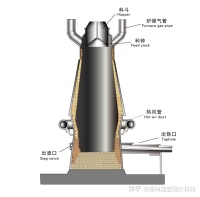
1.高爐澆注施工方案設(shè)計(jì)不合理
環(huán)向、縱向膨脹縫設(shè)計(jì)數(shù)量不夠。高爐運(yùn)行后,澆注料受熱,體積膨脹,互相擠壓,產(chǎn)生裂紋。應(yīng)預(yù)留充分的間隙來滿足膨脹要求,防止高爐貫穿,沖刷保溫層。澆注前碳磚面上涂刷防水炭膠涂層,防止耐火泥漿浸入填充材料內(nèi)。爐底澆注前在碳磚內(nèi)面粘貼 50mm 的耐高溫纖維板,七段冷卻壁下端粘接 30mm的耐高溫纖維板,風(fēng)口的大套部位和中套的上半圓采用 20mm 的纖維氈包裹住,中套的下半圓使用具有高強(qiáng)度的 100mm 厚聚氯乙烯泡沫板進(jìn)行包裹,澆注后燒出空腔,拆模后填充緩沖泥漿緩沖風(fēng)口下部的耐材襯體的膨脹。
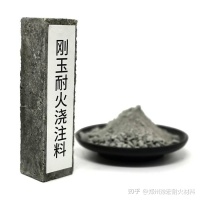
2.施工工藝不合理
(1)澆注料在攪拌時(shí)“灰水比”控制不好。加水量過多,澆注料成型后材料內(nèi)部氣孔率高,材料強(qiáng)度降低,自然凝固時(shí)間過長,養(yǎng)生時(shí)間加長。加水量太少,材料流動(dòng)性不好,振動(dòng)不密實(shí),容易留下氣孔、洞穴等,強(qiáng)度也將大大降低。
(2)攪拌時(shí)間和振動(dòng)時(shí)間控制不好。攪拌時(shí)間太短,材料混合不均勻,不密實(shí),強(qiáng)度降低;澆注料的澆注應(yīng)采用震搗機(jī)分層進(jìn)行震搗。振動(dòng)時(shí)間過長,材料易產(chǎn)生分層,細(xì)粉浮在表面,骨料沉在底部,導(dǎo)致材料強(qiáng)度降低易剝落。澆注料拌后30min內(nèi)用完,宜一次澆注到所規(guī)定的厚度和高度。澆注料施工應(yīng)在5℃以上的環(huán)境下進(jìn)行,因?yàn)闇囟忍?,材料不易凝固,即使凝固,也是一種假凝現(xiàn)象,澆注料一般應(yīng)連續(xù)進(jìn)行澆注,在前一層澆注料初凝前,應(yīng)將下一層澆注料澆注完。如施工間隙超過其初凝時(shí)間,應(yīng)按施工縫要求進(jìn)行處理。
(3)脫模時(shí)間控制不好。澆注料還沒有硬化就進(jìn)行脫模。應(yīng)在澆注料強(qiáng)度能保證其棱角不因脫模受損壞時(shí),方可拆除。承重模板應(yīng)在澆注料達(dá)到強(qiáng)度的70%時(shí)方可拆模。為便于脫模,澆注前所有模具的澆注面均應(yīng)涂一層機(jī)油。
(4)澆注料養(yǎng)護(hù)時(shí)間控制不好。鍋爐砌筑完后要有足夠的自然干燥期,使耐火層中大部分水分能析出,防止烘爐時(shí)大量水分不能及時(shí)排出,使耐火層爆裂和脫落。
(5)烘爐質(zhì)量控制不好。烘爐是將爐襯材料中自然干燥無法排除的游離水和結(jié)晶水排除,同時(shí)對(duì)澆注料進(jìn)行高溫固化以達(dá)到一定的強(qiáng)度。
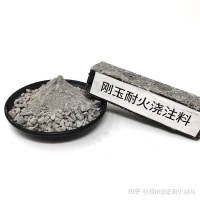
3.澆注料的熱震穩(wěn)定性能較差,材料質(zhì)量不過關(guān)
澆注料的熱震穩(wěn)定性能較差,劇烈的溫度變化很容易使之損壞。以回轉(zhuǎn)窯的冷卻帶(特別是窯口處)為例,該處不僅要受熟料不斷地磨蝕,而且還要不斷地受二次風(fēng)和窯內(nèi)高溫熟料的作用,每轉(zhuǎn)一圈,窯襯材料有時(shí)埋在高溫物料下,有時(shí)暴露在火焰下,造成襯料表面溫度隨窯的轉(zhuǎn)動(dòng)而發(fā)生同期性變化,溫度差達(dá)200℃以上,影響深度15~20mm,按照窯速3.5r/min計(jì)算,這種周期性溫度升降多次重復(fù)導(dǎo)致澆注料的表面層發(fā)生熱疲勞;如果冷窯,這種溫度變化更加劇烈。它們都是造成澆注料損壞的原因。檢修剔除時(shí)可以發(fā)現(xiàn),殘存部分的澆注料表面20~50mm深度范圍內(nèi)多呈現(xiàn)剝落、掉塊的現(xiàn)象,這主要是熱疲勞造成的損壞。
4.烘爐及高爐的運(yùn)行時(shí)的不正當(dāng)操作