在設(shè)計(jì)焊接工藝規(guī)程的過程中,需要著重考慮以下問題:
1、分析結(jié)構(gòu)的形狀和尺寸
在焊接構(gòu)件設(shè)計(jì)圖中,嚴(yán)格地規(guī)定了產(chǎn)品的幾何形狀、位置精
度和尺寸精度要求。在生產(chǎn)過程中,幾乎每一個(gè)加工環(huán)節(jié)都有可能引起零部件的變形,因此必須嚴(yán)格要求每道工序的加工精度,
保證不符合要求的焊件不轉(zhuǎn)移到下一工序。若出現(xiàn)精度超差的部件,則尋找相決辦法。要充分慮到構(gòu)件由于焊接所產(chǎn)生的變形,以及由于焊接收縮和矯正焊接變形引起的構(gòu)件尺才的縮小。從產(chǎn)品結(jié)構(gòu)方面人手,去估計(jì)有可能產(chǎn)生的焊接變形。
例如,薄板上焊接眾多加強(qiáng)筋的結(jié)構(gòu),由于垂直板平面方向的剛度小,焊接后容易產(chǎn)生波浪變形,我們可以首先進(jìn)行反變形,然后再焊接加強(qiáng)筋;對于細(xì)長桿件焊接結(jié)構(gòu),焊接后容易產(chǎn)生彎曲和扭曲變形,則可以采取對稱施焊的方法,以減小焊接變形;單面V形坡口的焊接變形比雙面X形坡口的焊接變形大,中厚板對接焊縫應(yīng)開雙V形坡口對接焊; T形截面的焊接梁,由于焊縫集中于中性軸的一 側(cè),焊后將產(chǎn)生彎曲變形,可以將兩根T形梁成對背對背剛性固定后再進(jìn)行焊接。
2、焊接接頭的質(zhì)量要求
焊接接頭的質(zhì)量包括接頭力學(xué)性能、外觀要求和內(nèi)部探傷質(zhì)量要求。對一般焊接接頭的質(zhì)量要求是,接頭的工作性能等于或略高于母材。在確保焊接時(shí),首先分析母材,從焊接冶金和焊接熱循環(huán)兩個(gè)方面,結(jié)合產(chǎn)品結(jié)構(gòu)特點(diǎn)和材料化學(xué)成分及供應(yīng)狀態(tài),分析采用什么焊接方法才能獲得成形最好的焊接接頭。然后根據(jù)所選定焊接方法的工藝特點(diǎn),合理調(diào)整焊接參數(shù)或采取些特殊的 工藝措施,可確保所產(chǎn)生的焊接工藝缺陷最少。
最后分析接頭的使用性能,盡可能地減少焊縫外觀缺陷或通過對焊縫進(jìn)行特殊處理,達(dá)到接頭較高的使用要求,如通過對焊縫進(jìn)行錘擊處理,則可提高接頭的疲勞強(qiáng)度等。
3、采用分步裝配焊接零部件
當(dāng)復(fù)雜構(gòu)件由眾多焊接零部件組成時(shí),每個(gè)焊接零部件在焊接過程中都會產(chǎn)生或大或小的焊接變形,如果將大量的零部件都組裝在一起,然后進(jìn)行整體施焊,產(chǎn)生的焊接變形將難以預(yù)計(jì),并且也很難保證每條焊縫在較好的焊接接位置施焊。所以,應(yīng)盡可能分步裝配焊接零部件,控制焊接變形。
在分步裝配焊接時(shí),將結(jié)構(gòu)適當(dāng)?shù)胤殖蓛簜€(gè)部件,分別加以裝配焊接,然后再將這些焊好的部件拼接成一體,這不但有利于控制焊接變形,而且能提高生產(chǎn)效率,為縮短生產(chǎn)周期創(chuàng)造了良好條件。
4、合理安排焊接次序,減少應(yīng)力集中
復(fù)雜構(gòu)件的焊接順序至關(guān)重要,如果焊接順序不合理,不僅使焊接變形難以修復(fù)。而且還會產(chǎn)生很大的應(yīng)力集中,對結(jié)構(gòu)的使用性能帶來安全隱患。所以,應(yīng)盡可能先焊接距離截面中性軸近的焊縫,由近及遠(yuǎn)地進(jìn)行焊接,如果焊縫對稱于截面中性軸分布,應(yīng)對稱施焊。
5、采用先進(jìn)的焊接工藝
采用先進(jìn)的焊接工藝是為了保證產(chǎn)品的質(zhì)量、提高生產(chǎn)效率、
改善勞動條件和降低生產(chǎn)成本。因此,采用先進(jìn)的焊接工藝或設(shè)備應(yīng)能滿足產(chǎn)品的技術(shù)條件和質(zhì)量要求,而且在生產(chǎn)過程中能夠保證產(chǎn)品質(zhì)量的穩(wěn)定。另外,所采用的工藝應(yīng)該是環(huán)保的,不污染或少污染環(huán)境,即使有污染也是可以治理的。所采用的先進(jìn)工藝應(yīng)該是具有一定的靈活性和柔性,在保證總體先進(jìn)的工藝水平下,使先進(jìn)技術(shù)與一般技術(shù)結(jié)合,達(dá)到總體工藝水平提高的目的。
隨著焊接自動化程度的提高,大的鋼結(jié)構(gòu)企業(yè)具有鋼板預(yù)處理生產(chǎn)線,對鋼板進(jìn)行搟平、打砂、預(yù)施涂料處理,可大大地提高鋼材的處理能力。目前鋼結(jié)構(gòu)零部件的形狀日趨復(fù)雜,尺寸精度要求越來越精確,采用傳統(tǒng)的手工劃線和手工氣割下料已經(jīng)不能滿足大生產(chǎn)需求,現(xiàn)代焊接車間備料工段一般都有 數(shù)控精密火焰切割、等離子弧切割、激光切割或水切制設(shè)備,對于形狀復(fù)雜的板件下料,它可以根據(jù)預(yù)先編制的程序,直接從鋼板上切割出所需要形狀和尺寸的零件,一般不再進(jìn) 行機(jī)加工就能夠直接進(jìn)人裝配和焊接工序。
還通過數(shù)控套料可以提高材料的可利用率,節(jié)約材料。對薄板的下料,采用等離子弧切割、激光切割或水切制設(shè)備,精度高、變形小,其優(yōu)勢更加突出。
6、選用的焊接工藝方法應(yīng)便于操作
焊接是整個(gè)生產(chǎn)工藝過程的核心工序,因此,首先應(yīng)分析產(chǎn)品
采用先進(jìn)焊接技術(shù)的可行性。只有焊接方法及其機(jī)被化和自動化水平確定之后,與之相適應(yīng)的焊前備料、裝配和焊后處理等工藝方法及其先進(jìn)性也大致可以確定。
目前規(guī)核工藝技術(shù)已經(jīng)發(fā)展到較高水平,基本上能實(shí)觀機(jī)核化、自動化和機(jī)器人爆接,對構(gòu)件采用自動焊方法的要求是:產(chǎn)品結(jié)構(gòu)上的焊縫數(shù)最要多、焊縫長且直或規(guī)則(如管子的環(huán)焊縫);坡口制備、組裝要符合公差尺才的要求,焊接坡口清理必須干凈;除了焊接設(shè)備外,一般還需要有焊接 變位機(jī)、滾輪支架、液壓矯形機(jī)械等自動化較高的輔助裝置的密切配合。只有這些要求都能滿足,采用自動焊才有可能。
7、易于保證熱處理質(zhì)量
焊件熱處理方法的選擇,應(yīng)考慮不同熱處理的要求及熱處理設(shè)備所需要的能源情況,,通常采用火焰加熱和電加熱兩種方法。
火焰加熱包括用氣體(煤氣、天然氣、液化石油氣等)、燃油、
煤的火焰加熱。火焰加熱的主要缺點(diǎn)是:工作條件差和熱效率低
(僅僅為20% ~30%)。但對大型球罐、圓筒形容器等,可采用氣體
火焰在內(nèi)部加熱,外部保溫的措施,這樣可以在現(xiàn)場進(jìn)行整體回火,并取得良好效果。
電加熱包括中頻加熱和工頻加熱兩種。可利用各種加熱用電阻絲、帶、片等元件加熱。電加熱方法的優(yōu)點(diǎn)主要是:
(1)容易實(shí)現(xiàn)自動化,溫度控制精度高。
(2)熱效率高,特別是采用陶瓷纖維絕熱時(shí),熱效率可達(dá)到
80%~90%。
(3)加熱均勻。
(4)清潔、無煙塵,勞動條件好。
整體熱處理時(shí),必須要保證加熱溫度的均勻性,并嚴(yán)格控制熱處理工藝,否則會導(dǎo)致由于加熱溫度不均勻反而使應(yīng)力增大。要根據(jù)焊接結(jié)構(gòu)的具體情況擬定熱處理規(guī)范,其中包括不同溫度區(qū)的加熱、保溫溫度及保溫時(shí)間、冷卻速度、測溫 點(diǎn)的布置及允許的最大溫差等。
以上是大概情況,對于具體焊接結(jié)構(gòu)應(yīng)具體分析,靈活應(yīng)用,盡量考慮全面些。
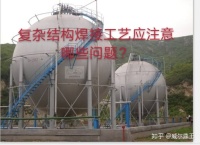